Case 1:
This case study delves into a distinguished enterprise specializing in the in-house manufacturing of Power Distribution Systems. This company trades their products on the international market and has been scaling up to meet the demands of their clients. In terms of scaling up and meeting the expectations of markets demand, this company started looking for a system to safeguard their data as well as handle most of their business processes from start to finish in a digital platform.
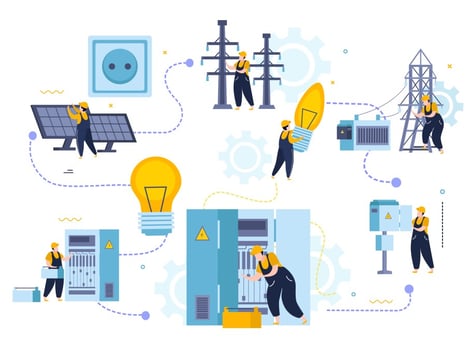
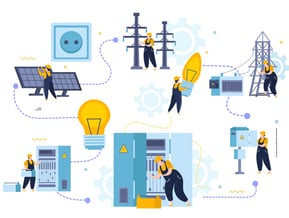
Company Overview:
Challenges Faced
Inability to effectively track work orders through various stages of production.
Lack of comprehensive visualization tools for monitoring stock levels across warehouses
Absence of a standardized data acquisition process on the production floor, leading to manual collection methods.
Deficiency in a centralized data centre for holistic analysis and predictive demand forecasting, resulting in data silos.
Anticipated challenges in managing escalated production levels, encompassing increased production costs, extended lead times, and traceability concerns.
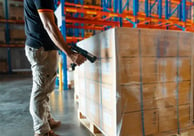
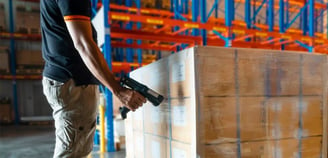
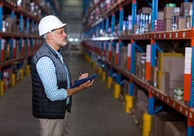
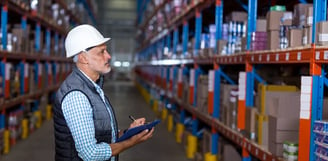
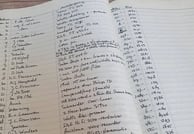
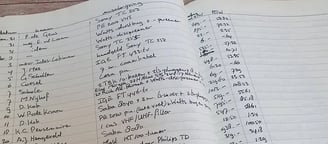
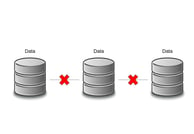
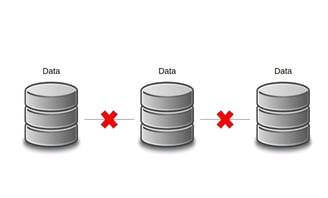
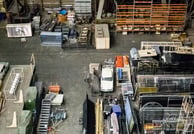

T-Robot Solutions Implemented:
Deployment of an Enterprise Resource Planning (ERP) system, inclusive of a robust Warehouse Management System, to optimize inventory handling.
Implementation of a Manufacturing Execution System (MES) to streamline and orchestrate -production processes.
Seamless integration of the new systems with pre-existing infrastructure to ensure operational continuity.
Provision of hardware solutions facilitating automated data collection and integration with the digital platform.
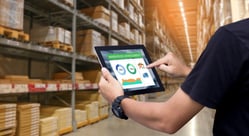
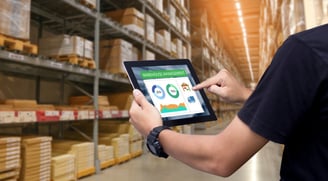
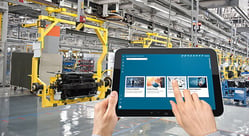
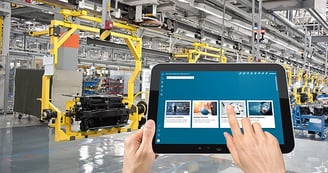
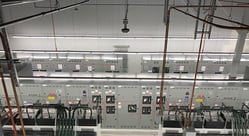
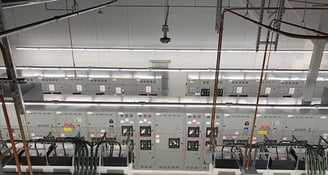
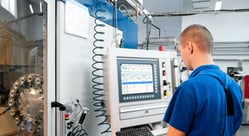
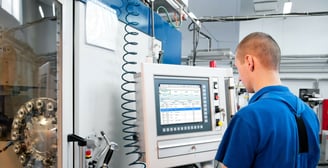
Benefits Realized from the Implemented System
Enhanced traceability of finished goods throughout the production lifecycle.
Optimized inventory management capabilities, fostering efficient stock control.
Automation of data acquisition processes, minimizing manual intervention and mitigating human error.






Preservation of data integrity through standardized digital protocols.
Establishment of a centralized database housing comprehensive operational data, facilitating informed decision-making.
Capacity for scalable production levels, enabling the company to meet evolving market demands with agility and precision.






Case 2:
Here is an insight on a company that offers comprehensive plastic manufacturing services, including injection moulding and blow moulding, to produce a diverse range of products such as plastic bottles and custom plastic components. With advanced technology and expertise, they deliver high-quality solutions to meet the unique requirements of their clients across various industries.
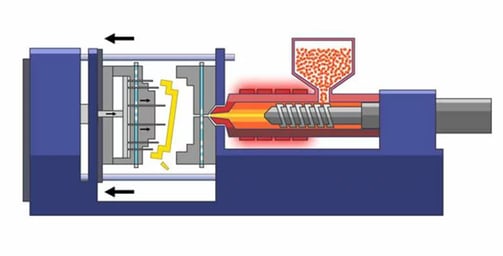
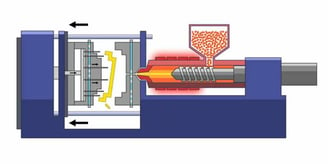
Company Overview:
Challenges Faced
There was no data being collected and stored.
Downtime of machines were quite common
Maintenance of machines that have broken down would run for long periods of time unmonitored
Market demand is increasing, and production can’t keep up
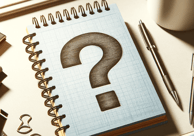
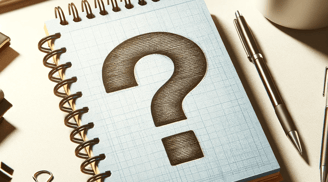
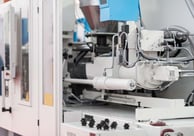
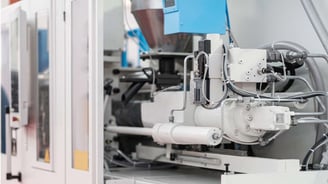
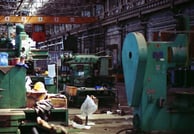
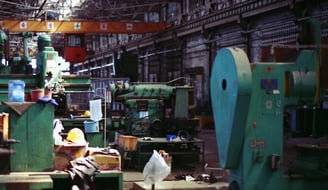
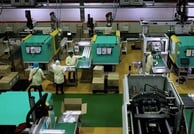
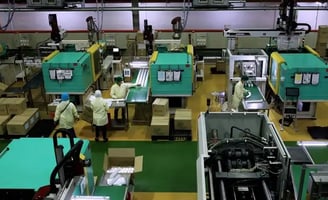
T-Robot Solutions Implemented:
Implementation of a Manufacturing Execution System (MES) to streamline and orchestrate -production processes.
Installed a monitoring system for the shopfloor and tools to monitor downtime of machines and the time required for maintenance team to fix the machine.
A customized dashboard that gives performance reports based on machines and by months.
Seamless integration of the new systems with pre-existing infrastructure to ensure operational continuity.
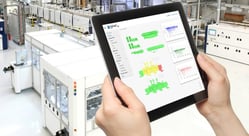
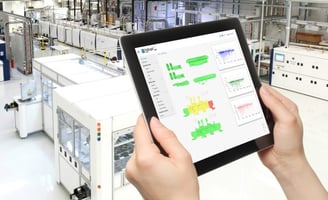
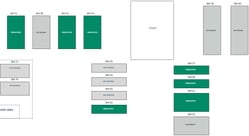
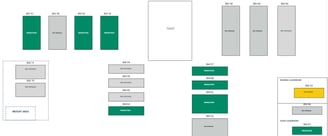
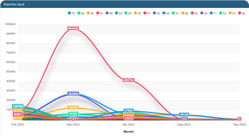
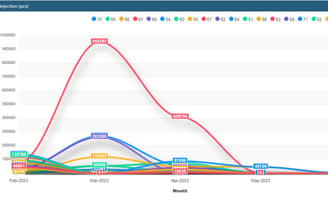
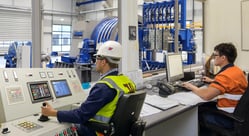
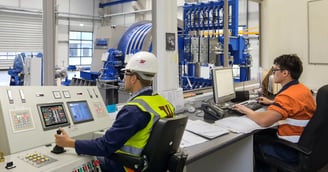
Benefits Realized from the Implemented System
Tracking of work orders were much easily handled
Data of rejected parts were collected automatically in a digital system
Product traceability allowed engineers to pinpoint faulty machines






Maintenance of broken down machines could be monitored visually and timed
The performance reports by machines allowed the production engineers to make decisions to add more of those types of machines or remove them.




Case 3:
Here is another example of a manufacturer specializing in eco-friendly furniture products. They are committed to sustainable practices and prioritize environmental conservation in their operations.
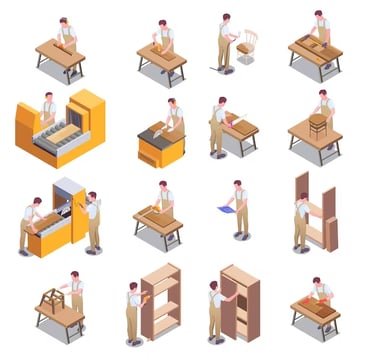
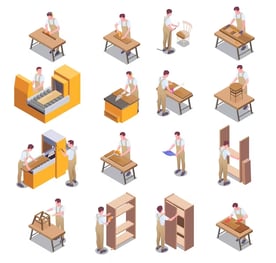
Company Overview:
Challenges Faced
Inefficient power usage tracking
Difficulty in tracing production output accurately.
Inventory management issues, particularly with tracking stickers not adhering properly.
Lack of visibility into the origins of wood used in furniture production.
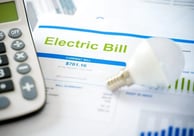

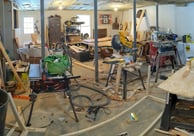
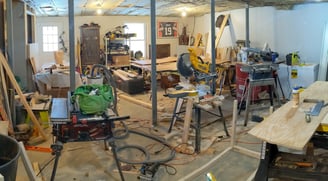
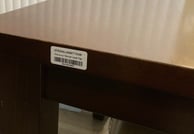
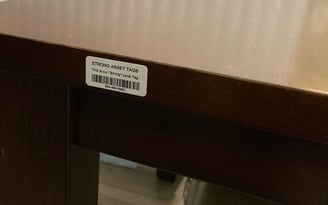
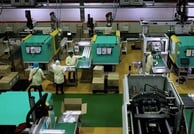
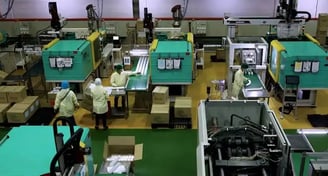
T-Robot Solutions Implemented:
Integration of IoT technology to trace production output and monitor power usage for two key CNC machines.
Enhancement of inventory management capabilities, resolving issues with tracking stickers
Implementation of a robust system to track the origins of wood used in furniture production, providing added service to clients by specifying wood types (e.g., Made from jati, kayu balak).
Production output, providing accurate insights into manufacturing performance and enabling better decision-making.
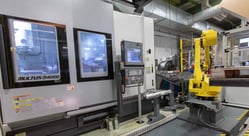
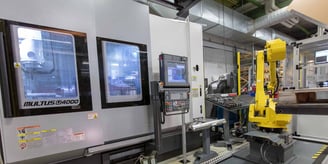
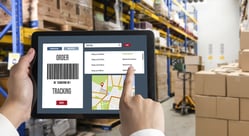
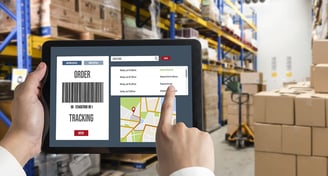
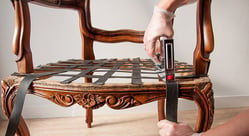
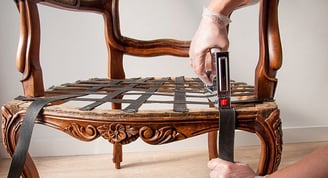
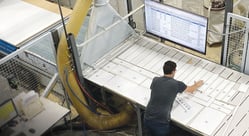
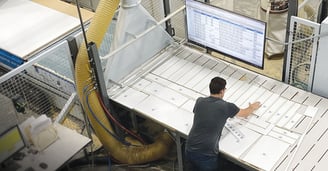
Benefits Realized from the Implemented System
Improved operational efficiency and cost savings through optimized power usage and streamlined production processes.
Enhanced traceability and transparency in inventory management, ensuring accurate tracking of materials and reducing errors.
Strengthened customer satisfaction by providing detailed information on the origins of wood used in furniture, aligning with their commitment to sustainability.








Increased competitiveness in the market by offering added value to clients and improving overall product quality and consistency.